個人向けワンオフパーツ製作ーキャリパーサポートのリバースエンジニアリング編 vol.2
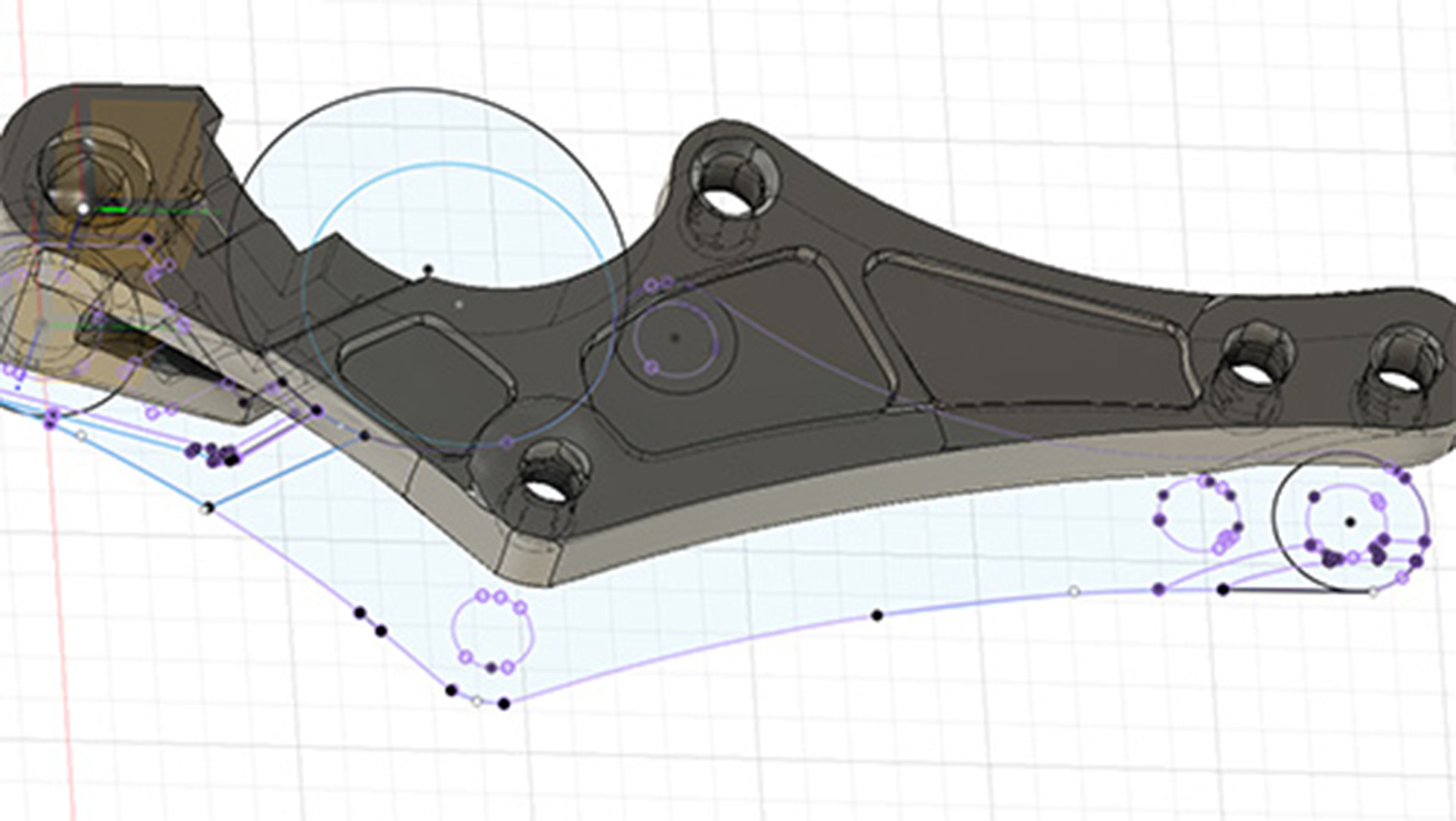
当社では、金属部品の特注品の多品種少ロット生産体制をBtoC向けにも提供しております。
(BtoC向けサービスについて詳しくはこちら)
今回は、前回に引き続き、一般消費者向けの事業でご依頼いただいた案件のご紹介です。
先日導入した3Dスキャナーを用いて、形状をスキャンし、図面作成後に加工まで行った事例です。
ご依頼は、バイクのブレーキキャリパーに取り付けるキャリパーサポートの製作という内容です。
今回の記事では、3Dスキャン後、図面作成の過程をご紹介します。
(BtoC向けサービスについて詳しくはこちら)
今回は、前回に引き続き、一般消費者向けの事業でご依頼いただいた案件のご紹介です。
先日導入した3Dスキャナーを用いて、形状をスキャンし、図面作成後に加工まで行った事例です。
ご依頼は、バイクのブレーキキャリパーに取り付けるキャリパーサポートの製作という内容です。
今回の記事では、3Dスキャン後、図面作成の過程をご紹介します。
本来、通常の3Dスキャナーでスキャンした場合、3Dスキャナーで取得したデータは点群データと呼ばれる膨大な点の集合体のデータとなります。
そのスキャンデータを下記の手順で加工する必要があります。
そのスキャンデータを下記の手順で加工する必要があります。
- 点群データをメッシュ化(ポリゴンデータに変換)。
- スキャンできなかった箇所の穴埋めを行い、穴のないメッシュデータを作成。
- メッシュデータからサーフェス面を生成。
- 面数を削減することで、軽量化されたCADデータに。
ただ、今回当社が導入したVL-700は、1~4の処理を自動で行ってくれます。
そして変換したデータをSTEP形式で吐き出してくれます。
吐き出されたデータがこちら。
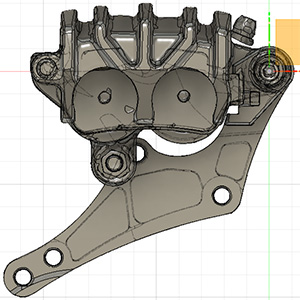
ある程度形になっているように見えますが・・・
↓のキャプチャをよく見ると、フェースが崩れて、複雑な面の組み合わせとして処理されている部分(タップ口元や溝部の壁など)があります。
これでは、機械加工に使えるデータではないので再モデリングする必要があります。
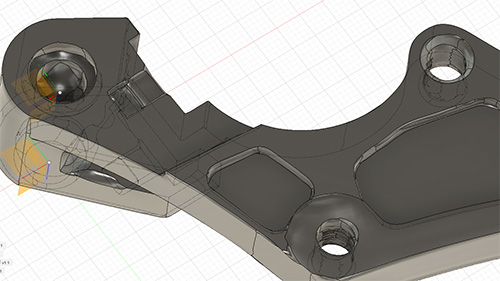
と、いうことで、こちらのCADデータをもとに、再度モデリングを行います。
いまスキャンしたモデルを基準面に投影し、投影された線をなぞりながら幾何形状として再定義した後に、そのつなげた形状を押し出してモデリングしていきます。
下のキャプチャの紫の線が、スキャンしたモデルを投影した線です。
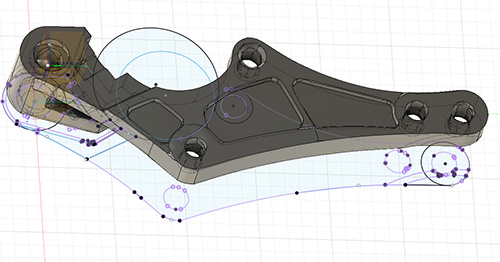
こうして、出来上がったのが↓のモデルです。
問題だったブレーキキャリパーへの取付穴の位置も、ブレーキキャリパーのスキャンモデルと重ねながら位置調整しました。
右上部にある溝位置や切り欠きの位置が元のモデルのままではブレーキキャリパーに干渉する問題等もありましたが、
お客様と打ち合わせしながらモデルを修正しました。
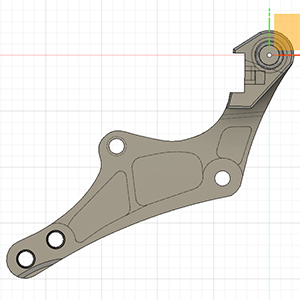
できた3Dモデルをもとに、今度は当社の製造現場に流すために紙の図面にも落とし込む必要があります。
紙図面化もそこそこの工数が必要なので、手戻りは許されません。
モデルの確認のため、今できたモデルを3Dプリンターで造形し、実物に合わせてみます。
1時間程度で造形完了です。
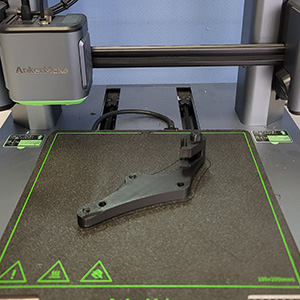
そして実際に合わせてみたのがこちら。
取付穴の位置も切り欠きの位置も問題なさそうです。
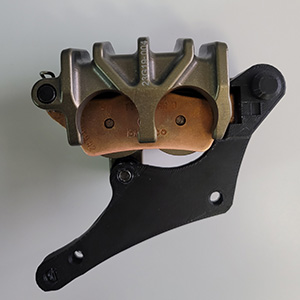
このモデルを、紙図面化します。
紙図面として出力して、加工における注意点などを手書きで追記していきます。
出来上がったのがこちら↓。(寸法情報等が記載してされているのでモザイク処理をかけています。)
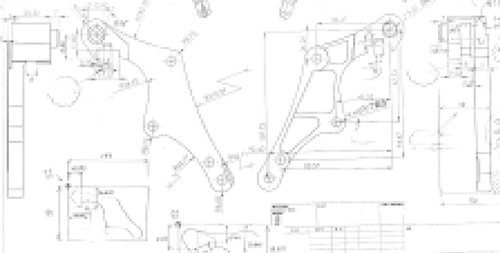
これで、加工に進む準備が整いました。
果たしてうまくリバースエンジニアリングできるのか・・・。
次の記事で製造過程を紹介します。
そして変換したデータをSTEP形式で吐き出してくれます。
吐き出されたデータがこちら。
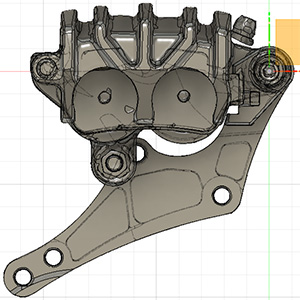
ある程度形になっているように見えますが・・・
↓のキャプチャをよく見ると、フェースが崩れて、複雑な面の組み合わせとして処理されている部分(タップ口元や溝部の壁など)があります。
これでは、機械加工に使えるデータではないので再モデリングする必要があります。
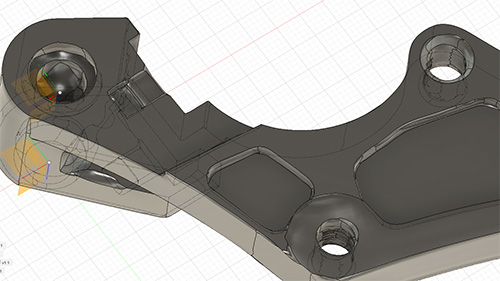
と、いうことで、こちらのCADデータをもとに、再度モデリングを行います。
いまスキャンしたモデルを基準面に投影し、投影された線をなぞりながら幾何形状として再定義した後に、そのつなげた形状を押し出してモデリングしていきます。
下のキャプチャの紫の線が、スキャンしたモデルを投影した線です。
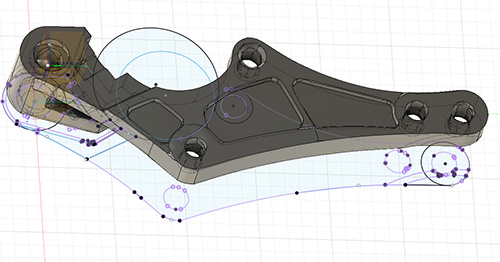
こうして、出来上がったのが↓のモデルです。
問題だったブレーキキャリパーへの取付穴の位置も、ブレーキキャリパーのスキャンモデルと重ねながら位置調整しました。
右上部にある溝位置や切り欠きの位置が元のモデルのままではブレーキキャリパーに干渉する問題等もありましたが、
お客様と打ち合わせしながらモデルを修正しました。
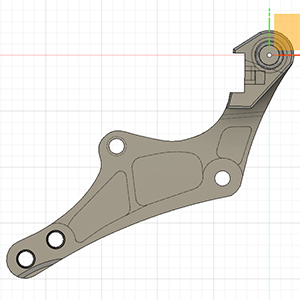
できた3Dモデルをもとに、今度は当社の製造現場に流すために紙の図面にも落とし込む必要があります。
紙図面化もそこそこの工数が必要なので、手戻りは許されません。
モデルの確認のため、今できたモデルを3Dプリンターで造形し、実物に合わせてみます。
1時間程度で造形完了です。
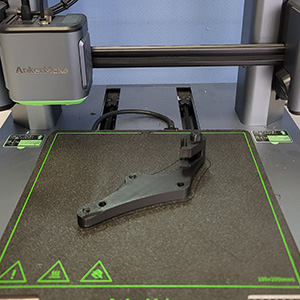
そして実際に合わせてみたのがこちら。
取付穴の位置も切り欠きの位置も問題なさそうです。
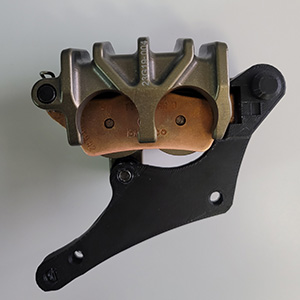
このモデルを、紙図面化します。
紙図面として出力して、加工における注意点などを手書きで追記していきます。
出来上がったのがこちら↓。(寸法情報等が記載してされているのでモザイク処理をかけています。)
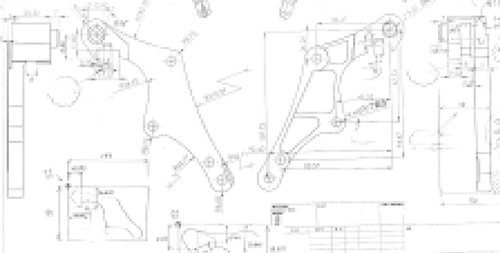
これで、加工に進む準備が整いました。
果たしてうまくリバースエンジニアリングできるのか・・・。
次の記事で製造過程を紹介します。